2025 Quarter 1 Safety Data
TRIR - 1.63
(Total Recordable Incident Rate)
TRIR currently 12.4% below 2024 year-end and reflects a 19.3% reduction from February to March which indicates a trend in the right direction.
LTIR - 0.67
(Lost Time Incident Rate)
LTIR is currently 26.4% higher than 2024 year-end so there is room for improvement but there was a 21.4% decrease from February to March which demonstrated our ability to quickly implement improvement and shift trends in the right direction.
“Good work and results improving with good numbers by the end of the quarter. Let’s keep up the current momentum!”
- Mark Burgess, President and CEO
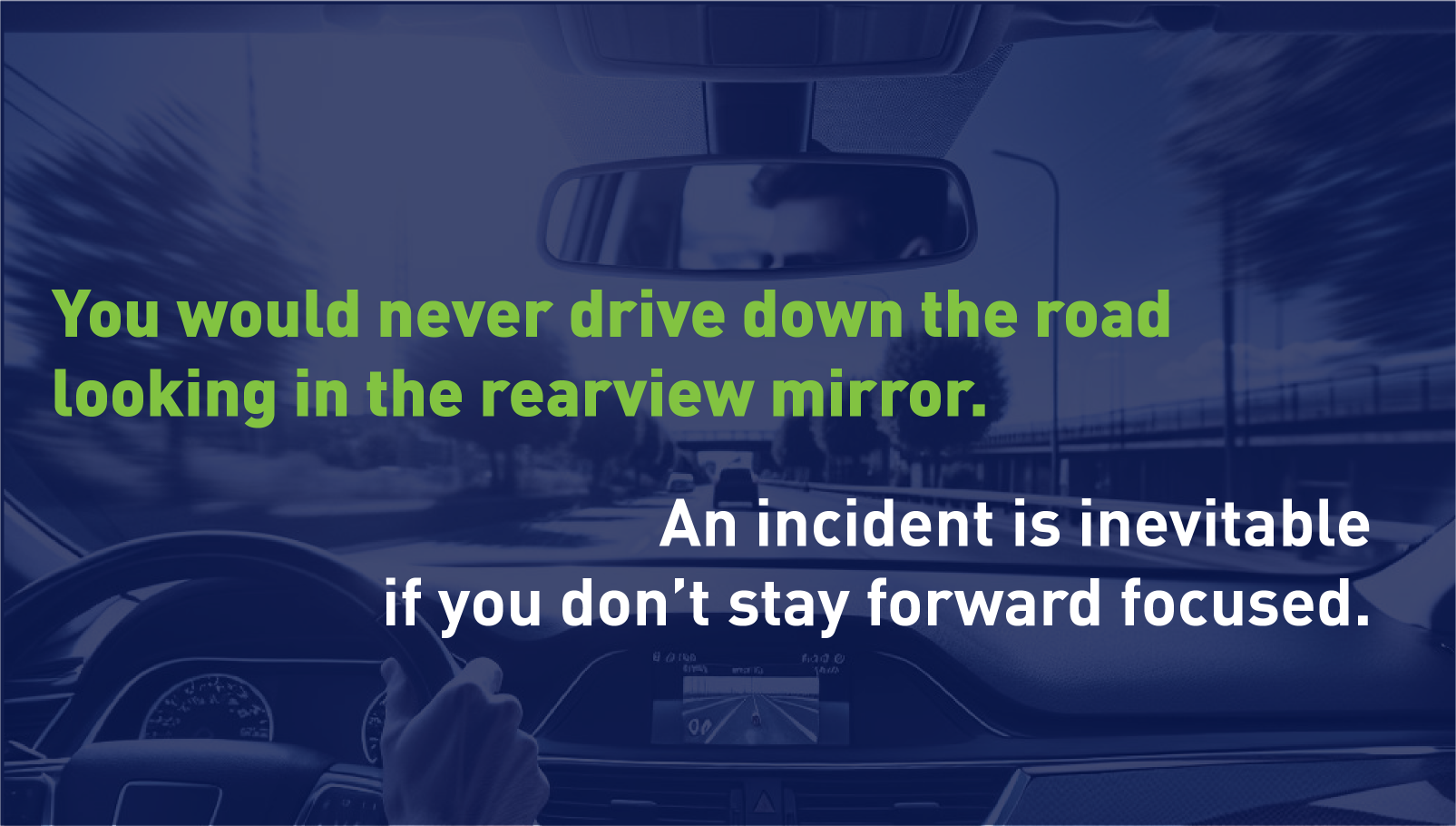
Business Unit Shout-outs:
Small Packaging
Both NASP divisions are trending below industry averages for plastics and metal manufacturing. As of end of February, our TRIR and LTIR compared to industry average means that we had 199 fewer employees injured and 99 fewer employees with a lost time injury than if we had been at the industry average. That’s equal to the entire employee population at some of our facilities. There are real people behind the data whose lives are protected when we commit to safe workplace practices.
Industrial Packaging
NAIP facilities performed a safety stand down on May 5 to address current safety performance that is below expectations. The stand down focused on reminding employees of their responsibility to work safely and bring attention to safety issues and their right to request training and refuse unsafe work. “While we do not question our employee’s commitment to safety and our ‘Dive to Zero’, we believe current performance warrants taking a moment to reflect and refocus,” commented Rick Capps, NAIP Director of Environmental Health and Safety.
International
MIPS is developing an intranet database for safety instructions that can be accessed and reviewed by individual employees. After reviewing the instructions, employees can complete an assessment to verify that the topic has been adequately communicated and to document understanding. Content will focus on specific topics and can be explored in more detail based on location. The database will be initially provided to locations in Germany and will include translations to improve the accessibility for non-German speaking employees. “This database will enhance the ability for individual employees to access important safety information on an as needed basis,” commented Oliver Lohmann, Safety Specialist – Europe.
Driving Safety: Mauser Transportation Fleet
In addition to safety within our facilities, Mauser is committed to the safety of the drivers in our private fleet and those they encounter on the road. During Q1 this year, Mauser drivers received 15 clean DOT roadside inspections*. These drivers are:
Juan Penaloza (x2)
David Perez
Faustino Tamayo
Malik Jones
Shanell Sipp
Marcus Wiley
Titus Balkuty
Luis Lebrun
Francisco Blancas
Oyd Crosby
Dwayne Barnes
Gustavo Gonzalez
Jeffrey Krites
Kenneth Wolters
Francisco Blancas