At Mauser Packaging Solutions, it is our ethical responsibility to ensure that each employee goes home safe, every day and each one of us shares in this responsibility. The importance of safety is greater than numbers and metrics but reviewing key indicators enables us to track our safety performance and progressing in the right direction to having a safe work environment.
Through the first quarter of 2024, Mauser had a decrease in the Total Recordable Incident Rate (TRIR) and Lost Time Incident Rate (LTIR) compared to 2023 year-end. NASP significantly decreased LTIR with 1 lost time case in Q1 resulting in only 6 lost days compared to 426 lost days in Q1 of 2023. NAIP finished Q1 with a 60% improvement in TRIR, 78% reduction in first aid cases, 121% improvement in near miss reporting, and 102% improvement in audits and worker observations compared to Q1 2023. MIPS continued to perform well in regard to safety with just seven incidents during Q1.
While we continue to see incident frequency trend downward (TRIR), we are also seeing a reduction in the severity of incidents decrease. Combined with other indicators, these trends indicate that we are making a difference and making our workplace a safe environment for employees. “In addition to a general increase in safety awareness, I credit this improvement to worker observations, Stop-Call-Wait, and our Life Saving Rule policy. I also give credit to our case management and investigation efforts, including in-depth investigations of incidents that are below the ‘recordables’ threshold, including near-misses,” commented Allen Coppolo, NASP Environmental, Health and Safety Director.
View the infographic below for a more detailed look at Mauser’s safety performance for the first quarter of 2024.
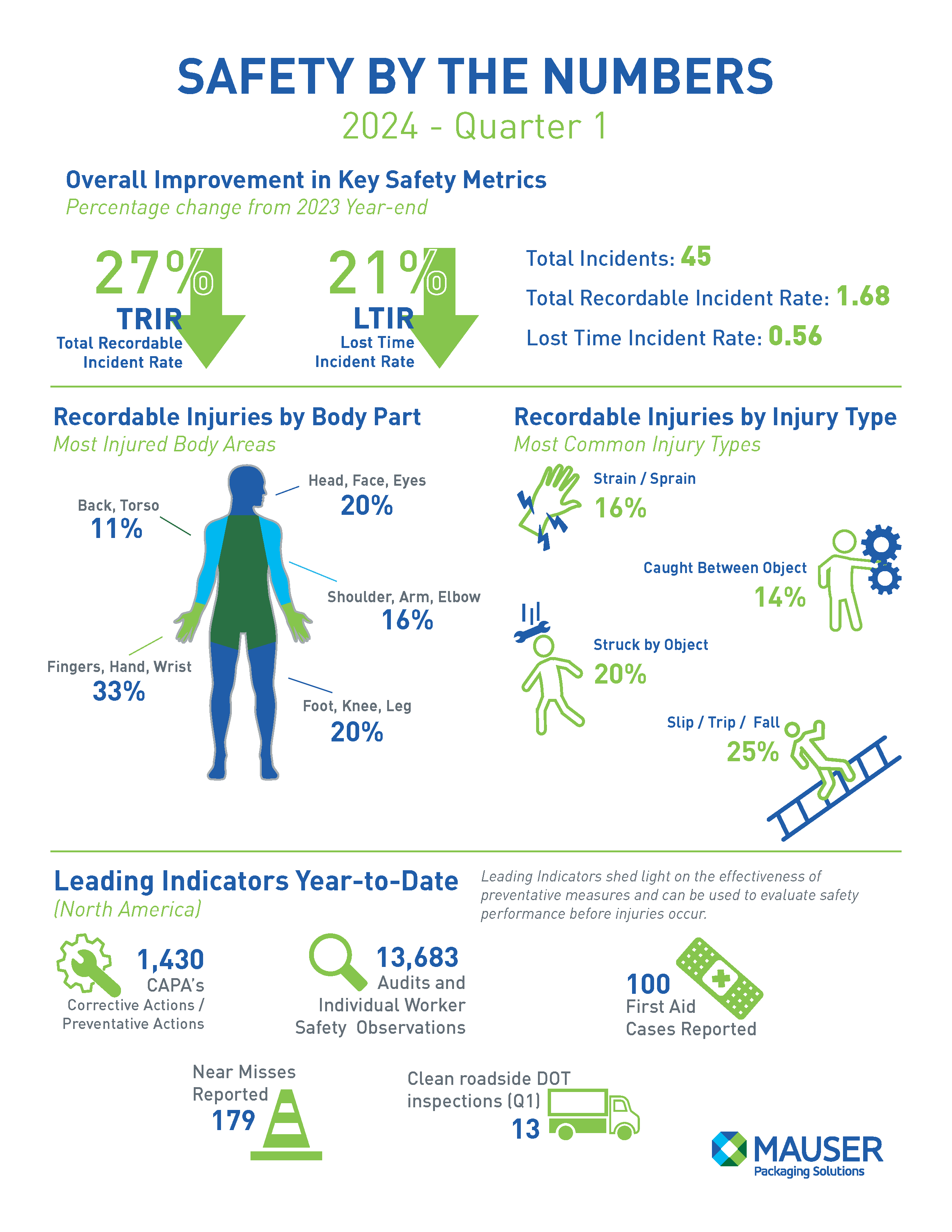
In addition to safety within our facilities, Mauser is committed to the safety of the drivers in our private fleet and those they encounter on the road. During Q1 this year, thirteen drivers received a clean DOT roadside inspection*. "These clean inspections are due to their commitment in making sure their pre and post trips are thorough, so they do not take non-compliant equipment on the road," commented Dan Kraemer, Regional Safety Manager.
These drivers are Gustavo Gonzalez (Roseville, Calif.), Jose Blancas (Roseville, Calif.), Michael Cross (Cleveland, Ohio), Julio Diaz (Seattle, Wash), Grant Ewell (Baltimore, Md.), Arthur Gehler (Cincinnati, Ohio), Morris Manning (Zellwood, Fla.), Dwain Campbell (Cincinnati, Ohio), Miquel Soto (Roseville, Calif.), Gustavo Gonzalez (Roseville, Calif.), Rafael Ortiz (Zellwood, Fla.), Grant Ewell (Baltimore, Md.), Daniel Cochran (Columbus, Ohio).