Launched in March, Mauser Packaging Solutions’ Plant Manager Engagement Workshop helps participants engage with employees and drive culture at facilities. While the workshop focuses on a variety of topics, a significant portion of the workshop centers around building the right safety culture. “Every other aspect of engagement is irrelevant if our leaders aren’t developing a culture that values safety above every other business or operational priority,” commented Matt Ralph, workshop facilitator and former Langley, BC, Canada Plant Manager.
The Workshop is designed to be highly interactive with participants learning from each other as much as they do from the material or facilitator. The open dialogue and free-flow conversations are intended to generate a social network among plant managers that in return should be a valuable resource used to create safer and more efficient work environments. Through team building and exercises, participants gain exposure to ideas that are being implemented at facilities across the Mauser Packaging Solutions enterprise and in return leverage success ideas.
Some ideas that have been shared during the first thee workshops include:
Life Saving Rules Magnets on Machines and Equipment
Shared by Adrian Gunter (Cedar City, Utah, NASP)
The Cedar City, Utah facility add magnets to machines and equipment that remind employees of the Life Saving Rule(s). By providing this visual, employees are constantly reminded of the commitment we have as a company and as individuals to operate safely.
Brown Bag Idea Sharing
Shared by Jemal Johns (Chicago, Illinois, NAIP – Fiber)
Periodically, “Brown Bag” idea sharing are held at the Chicago Fiber facility. Brown paper bags are used to create a space for employees to post ideas or suggestions for improving safety. The facility also sets a goal for receiving potentially actionable ideas and reward employees with a meal or company merchandise for meeting the goal. “For this activity to be successful, leadership must be committed to following through with implementing ideas and suggestions, so employees recognize that their submissions are taken seriously and implemented where able,” commented Jemal Johns, Chicago Fiber Plant Manager.
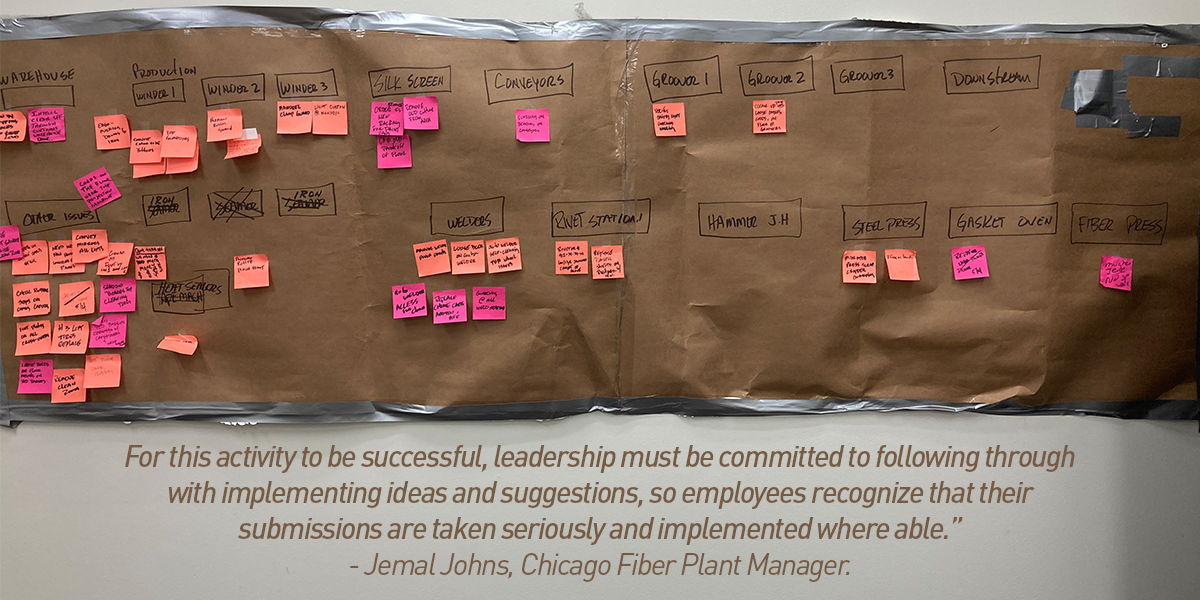
Safety Climate Assessment Tool (S-CAT)
Shared by David VanVoorhis (Hutchins, Texas – NAIP)
The Safety Climate Assessment (S-CAT) is a free online tool that facilitates the assessment of organizational and workplace safety climate. Originally designed to gauge the safety climate in construction organizations, the tool can be used by companies in other industries. Through the assessment, users respond to 37 separate items across eight safety climate factors. Responses indicate an organization’s safety culture as inattentive, reactive, compliant, proactive or exemplary for each item. The Hutchins, Texas facility recently had about 50 employees complete the survey to provide a baseline of the facilities safety culture. Future administrations of the survey will allow the facility gauge improvement compared to the initial baseline. “This tool provides us with an objective measurement of our safety culture which can be difficult to quantify outside of incident rates. This gives us a much better metric to gauge how our employees feel about safety in our facility,” commented David VanVoorhis, Hutchins, Texas Plant Manager.
Happy Meter
Shared by Matt Ralph (Langley, BC, Canada, NASP)
The Langley, BC Small Packaging facility has installed an electronic device called a “Happy Meter” at the employee entrance to receive quick feedback from employees on a variety of topics including safety. The questions asked by the Happy Meter are periodically changed and employees provide their response with a simple tap of a button. Employees also provide text responses that give more specific feedback regarding the current question. This allows for simple and timely tracking of how employees feel about their workday. Safety related questions make facility leaders aware of day-to-day changes on the production floor that may make employees feel less safe and could lead to future incidents.
These are just a few of the tangible examples that Plant Managers are sharing during the workshops. Other ideas include safety newsletters, enforcing GEMBA walks, improving orientation process, ways to implement improved safety training and much more.
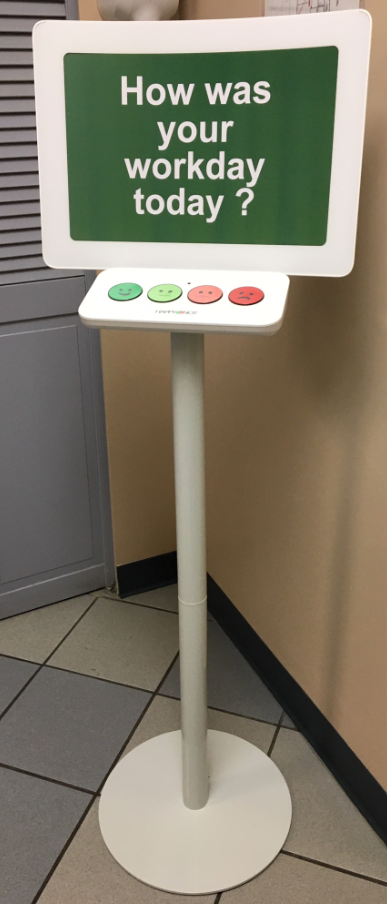
“The relationships being built among Plant Managers during the workshop is invaluable. Having a network of peers to learn from and reach out to for assistance improves each managers ability to lead their employees more effectively. The open dialogue and sharing of ideas definitely helps make our workplaces safer as managers learn from the successes of other facilities."