The collection and delivery of used containers to reconditioning facilities is a key link in the circular packaging life cycle that is a core element of Mauser Packaging Solutions’ commitment to sustainable packaging solutions. To improve efficiency and management of the collection and delivery process, Mauser Packaging Solutions is implementing a new inbound order entry and tracking system that will provide better internal visibility of this process and enable better customer service.
The new Service Manager system focuses on providing accurate data for 5 key milestones during the packaging collection process – receipt of request, pick-up, delivery, grading entry and invoicing. Under the current state, customers send an email when used containers are ready for reconditioning. The recipient of that email manually identifies the customer in an Access database, determines the facility to receive the containers based on physical proximity and facility schedule, and submits the order to the Transportation Management System (TMS) to secure a carrier for the delivery. The carrier selected for the transport then manages the pick-up of containers from the customer and delivery to the processing facility with little visibility. Once a container is at the facility, it is examined to determine the filling contents and current condition so a grading can be assigned which determines whether a container is suitable for reconditioning, is ready to be recycled or must be discarded. Currently, data entry for each step of this process is done manually making it hard to ensure accurate, up-to date information is readily available for our customers, as well as our operations and customer service teams.
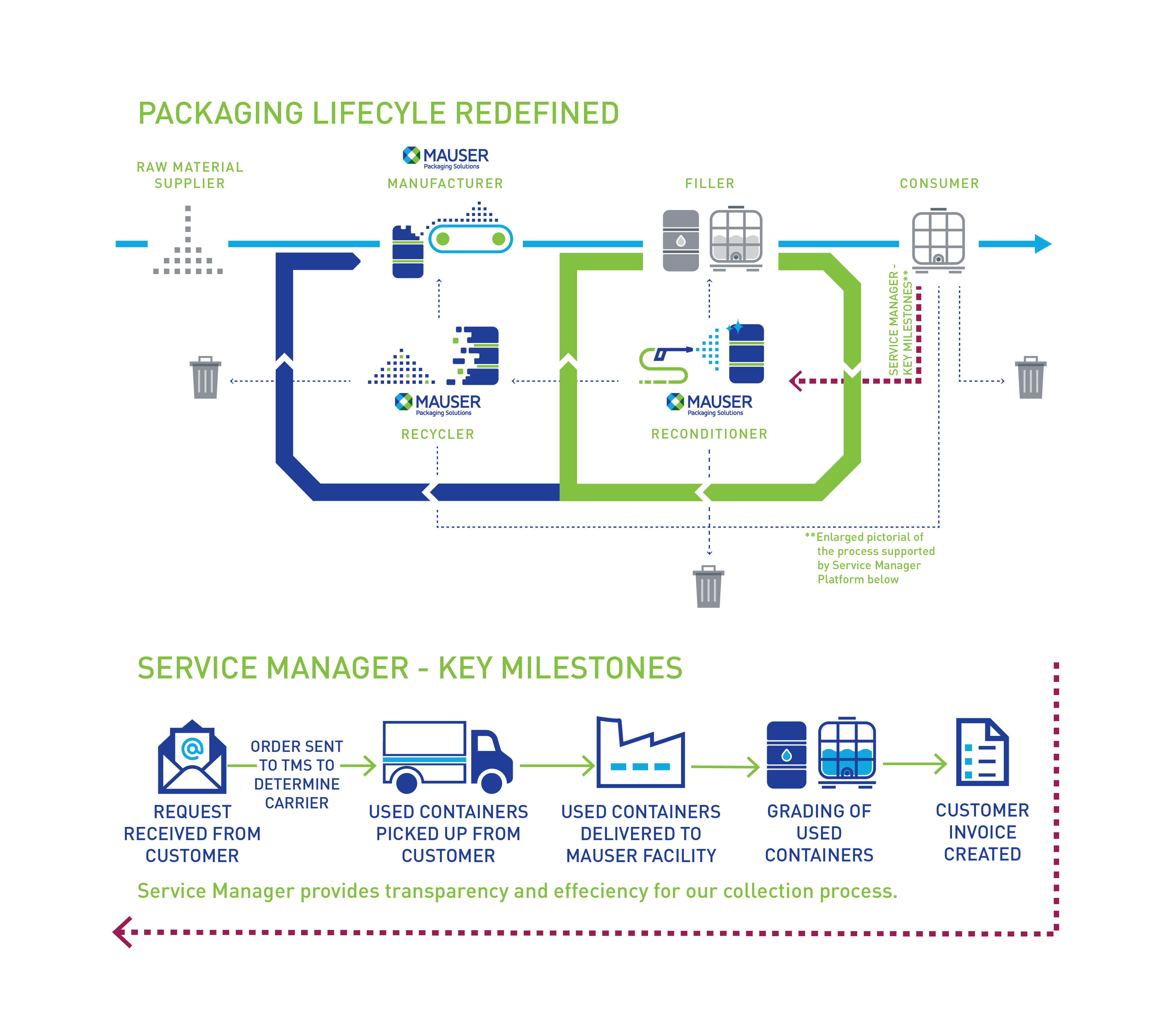
Click image to view .pdf version.
By transitioning to a new, more modern Service Manager platform, we will improve data integrity and workflow efficiency. The current system is roughly 20 years old, has significant manual data requirements and is unable to accommodate growth of our reconditioning business. Under the new system, our existing TMS (CTSI), container grading (IBM-Rapid) and invoicing (Solomon) systems will feed data to a central database which will provide easier and more transparent access to information. The new system will also provide reporting tools that will streamline current reporting processes, increase reporting capabilities and improve overall visibility.
The process of cleaning up customer information and identifying a more robust platform began in 2021. The new system went live earlier this month. Currently the National Inbound team is utilizing the system for all plastic or mixed container pickups. Once the initial implementation phase is successfully completed, Mauser plans to expand the system to additional users and capabilities to further stream line and standardize this area of the business.
“We do a great job at manufacturing new product and at reconditioning and recycling used containers, but we historically don’t do a great job at picking up or monitoring open requests for our customers. The new Service Manager system changes that.” commented Neil Pellicci, Director of Customer Service.
"We do a great job at manufacturing new product and at reconditioning and recycling used containers, but we historically don’t do a great job at picking up or monitoring open requests for our customers. The new Service Manager system changes that."