The facility routinely encountered blockage in the screen of the drum shredder grinder due to purges running through the machine that are too hot. This material would collect on the screens eventually causing a blockage. Clearing the blockage required maintenance employees cutting and burning the plastic off the screen. This process could take two maintenance employees 2 days to complete and creates safety risks from the use of torches and cutting instruments as well as generating fumes from burning plastic.
To identify material that should not enter grinder, a sensor was installed on the belt that feeds material into the shredder. The sensor detects if material is too hot or too cold to run through the machine and stops the belt before the material enters the screen. This allows employees to remove the material and avoid a build-up of blockage on the screen. A counter was also added to the sensor to track the number of times the sensor stops the belt. Instillation of the sensor took once maintenance technician approximately 3 hours to install and has successfully stopped material that is too hot from entering the machine aver 270 time since October 25.
The cost to purchase and install the sensor will be offset by the saved labor cost of preventing just one blockage. This technology also enables maintenance techs to reduce the number of times they must complete a task that poses safety risks and enables them to spend that time on other value add tasks. Following further evaluation and feedback of this project, this technology could be installed on other machines and in other facilities.
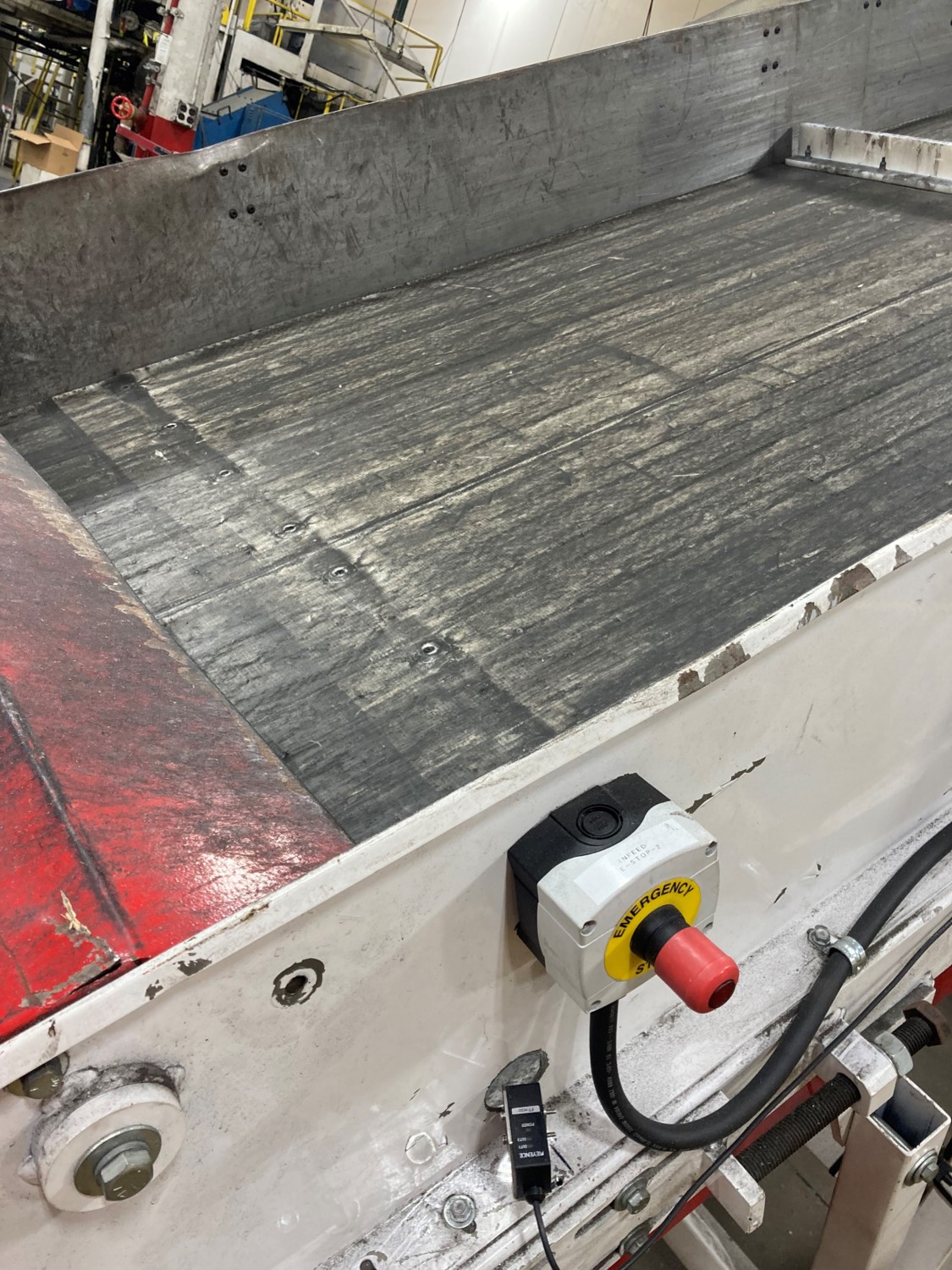
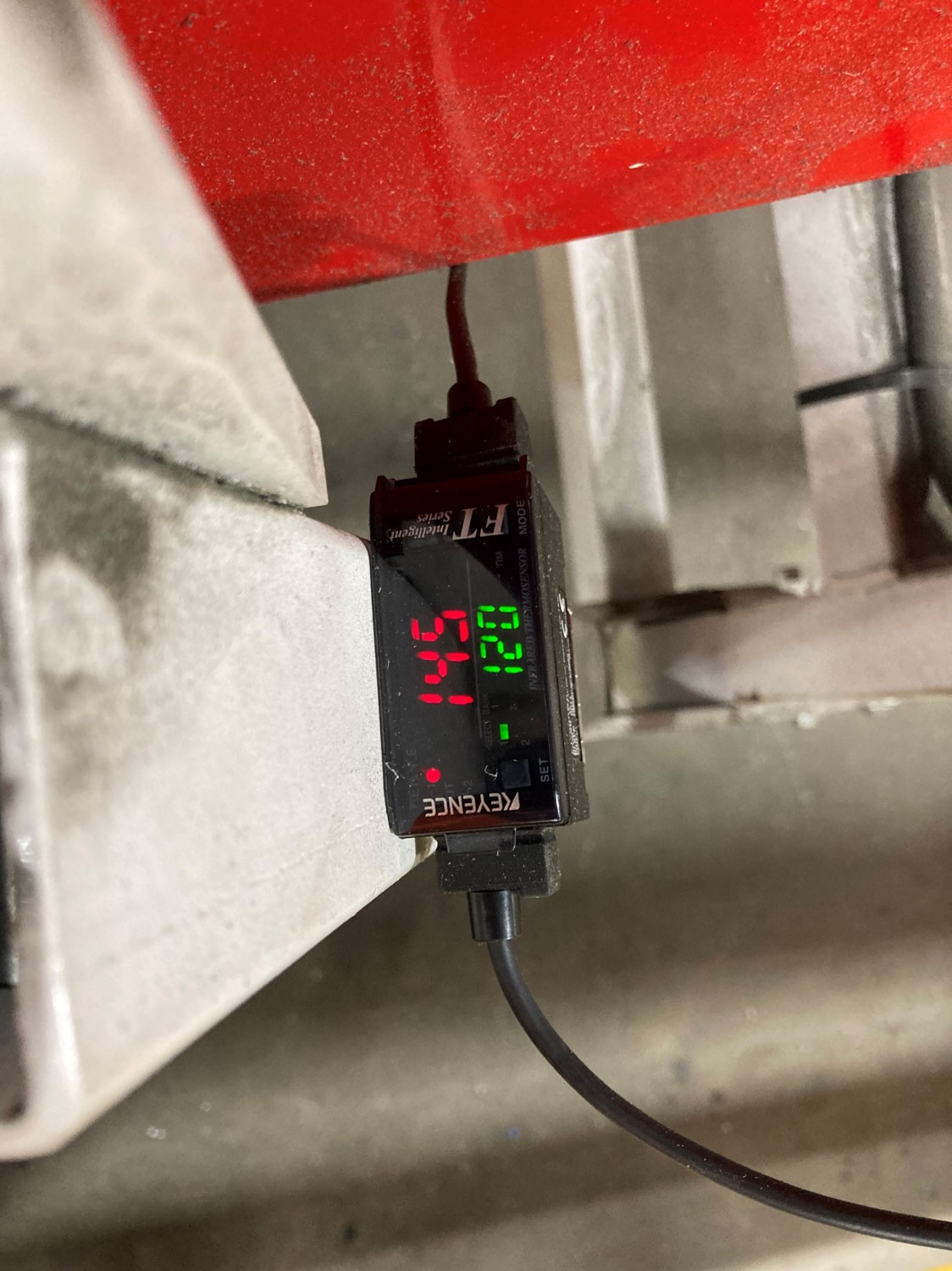
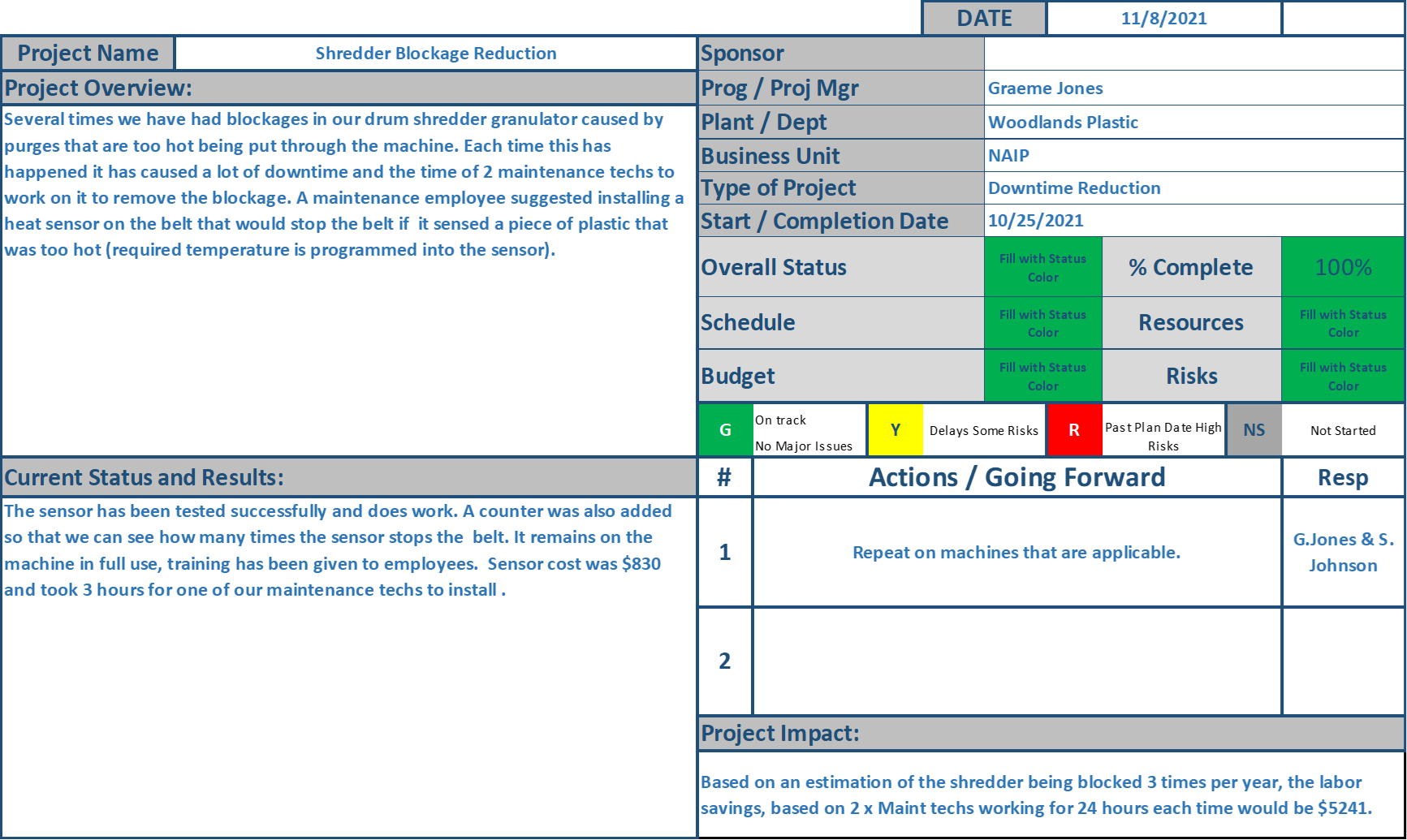