Our new Industrial Solutions facility located in Hutchins, Texas increases efficiency and provides a competitive advantage for large packaging and reconditioning operations.
The Hutchins facility, located in the metro-Dallas area, began manufacturing and reconditioning operations in June 2020 and will continue to ramp up through early 2021. When fully operational, the state-of-the-art facility will become home to the Kemp, Texas reconditioning operations and IBC blow molding. The current Kemp facility will continue operations through the end of 2020.
Advantages of the Hutchins facility include:
Increased safety and efficiency
Manufacturing and reconditioning operations are housed under one roof at the new state-of-the-art facility. By eliminating employee exposure to the elements, as well as the conditions that may occur when reconditioning processes takes place outdoors, employees will no longer need to work on muddy terrain which can be slick causing slips, trips, and falls.
Freight Cost Savings
Centralizing large packaging and reconditioning operations reduces the transportation of bottles between Mauser Packaging Solutions locations and thus reduces freight costs. Prior to the Hutchins facility opening, many of the bottles reconditioned in Kemp were shipped from Houston. Now, bottles can be transported within the same building.
Water treatment cost savings
The Hutchins facility is obtaining a permit to discharge water through the city as opposed to sending discharge water to a landfill or water treatment plant. This process improvement should deliver significant savings in water treatment costs.
Improved transportation logistics
Located in the Dallas-Fort Worth Metroplex, the facility is easily accessible to major highways and is conveniently located to two major airports. Proximity and convenience to transportation provides a competitive advantage for shipping and for customers visiting the facility.
Implementation of modern technique and technology
Large Packaging operations will be conducted using a state-of-the-art blow molder. In reconditioning, the manual deconstruction process will be automated using a multi-robot “monster” making the process safer for the employee. The monster contains three robots that cut the tote during the reconditioning process ultimately leading to the tote being recycled.
The new modern manufacturing site will serve as a blueprint for other dual reconditioning and large packaging facilities supporting the “One Mauser” strategy.
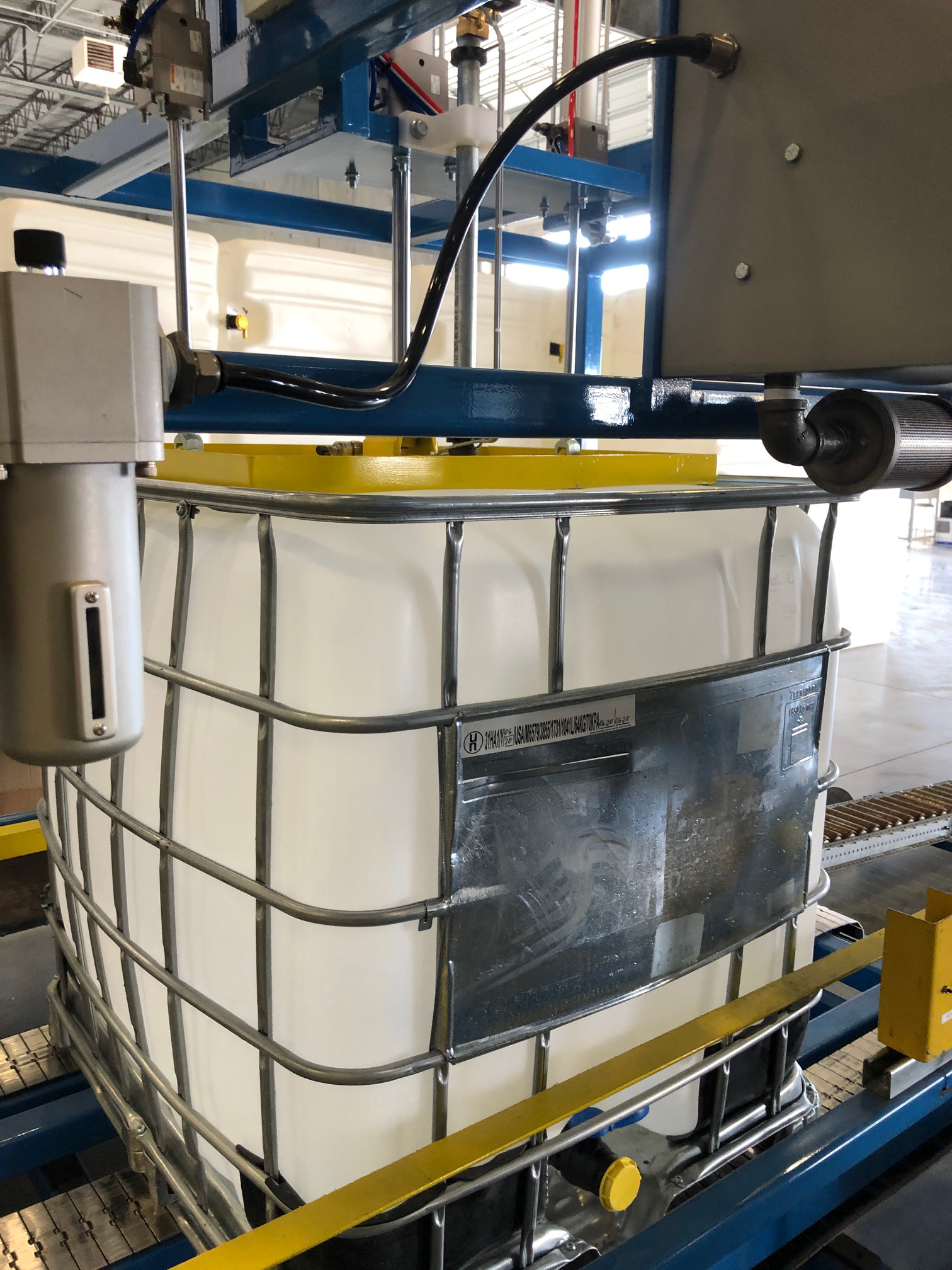
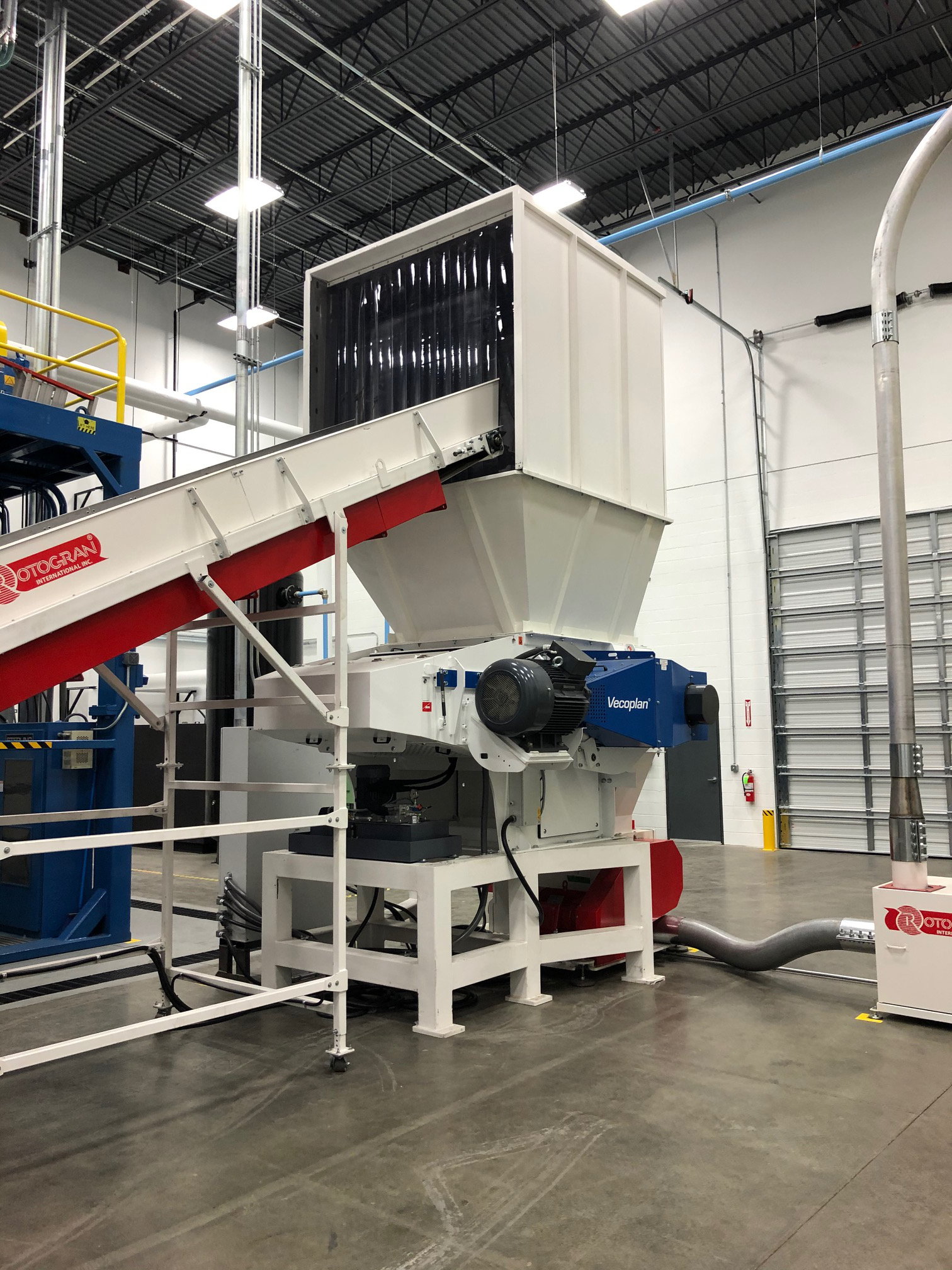
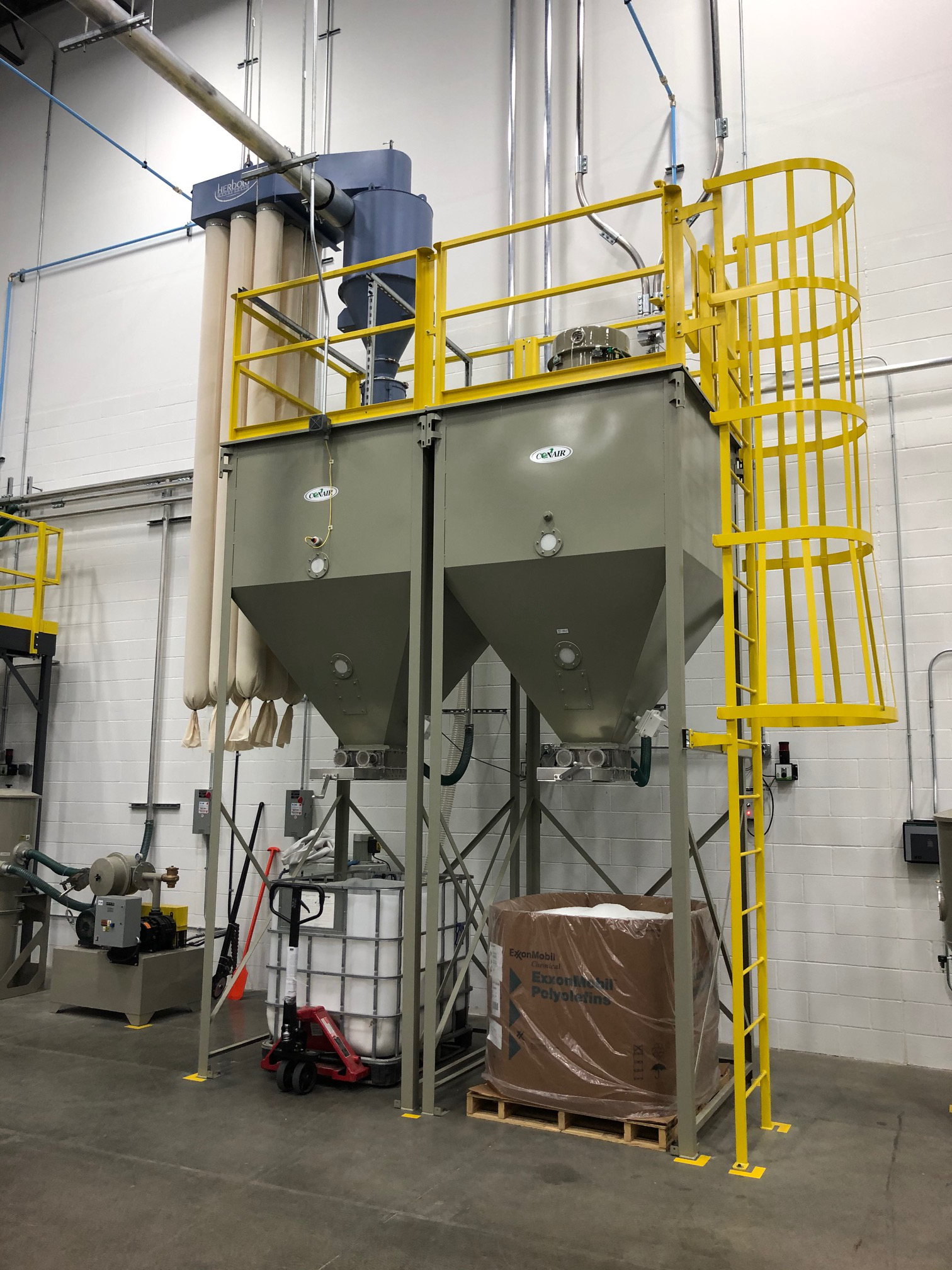
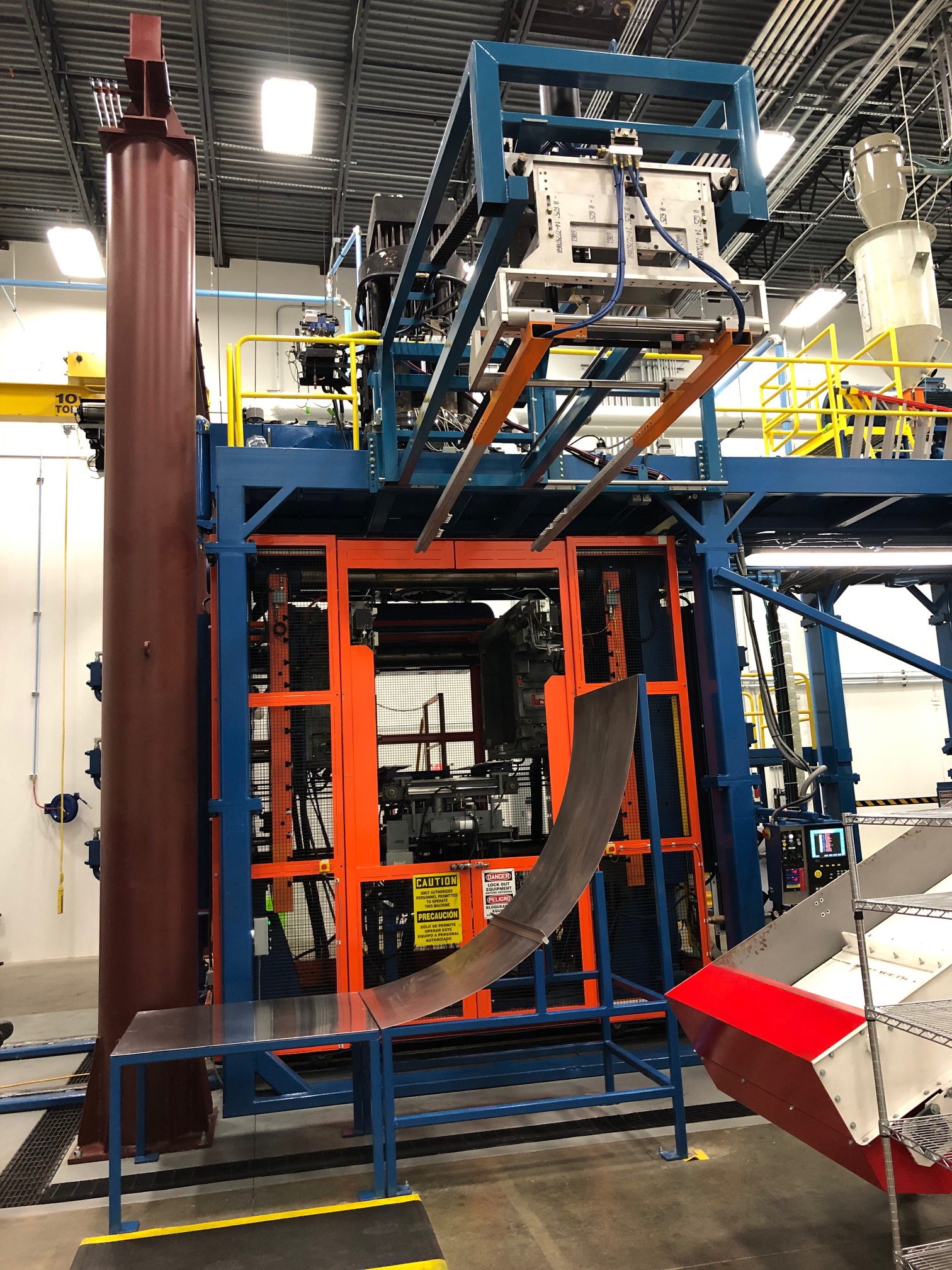